Tim,
I have used a light curtain to slow down a UR3. The output of the light curtain is an input to the robot. Then using that input as a trigger for a thread to slow the UR3 down from 100% to 10%. You can do the same thing with a safety mat or a safety scanner.
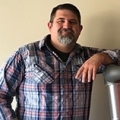
You can also have these input directly into the safety controller using the configurable inputs, then you can use reduced mode and set lower speeds, forces, moments, etc that are activated when the safety system is active. You can also plug directly into the safety system and have the robot physically stop moving when the safety system is active and then resume as soon as the signal is returned to normal. We have used this with safety mats to stop motion while someone is walking through the area and then automatically return to work once they have passed through.
To do the auto stop/start you just wire the safety output into the safeguard stop of the controller
If you want to use the thread route realize that this is technically not safety rated as there is no redundancy to the method and there is no guarantee that it would work every time unlike using the safety controller built in to the robot. You will need to call the speed slider using a TCP socket but here is the instruction on how to do that.
@Tim_Smith
We recently tested some light curtains for a client. So we decided to try the reduce mode of the UR. The setup was so easy. The light curtains that the client had were Reer Light Curtains. They have a way that you can wire them out such that they are in AUTO RESET mode. This is what we used in the video below. Then we hooked up the light curtains output to inputs of a safety relay. We then wired the output of the safety relays to the safety inputs of the UR controller. Then in the SAFETY setting of the UR we simply assigned the values of the plugged inputs to reduced mode. So in the video you see the robot going at roughly 3000mm/s and then switching to about 450mm/s when the operator moves his arms across the curtains.
https://youtu.be/KiN-N1a64w4
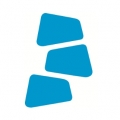
@matthewd92matthewd92 said:...or use safety relays. You would need two relays. You would wire the A channel from both into one relay, B channel from both into the other relay. Then wire one output from each relay to the safeguard circuit...
Hello Matthew, I should connect two light curtains and thee RFID-door-switches to an UR5e. Each safety device should be connected to an safeguard input. My mistake was, that I thought that I can configure the safety inputs of the controller as safeguard-stop inputs.
Have you an little schematic of the relay connections? I don't understand your explanation.
Thanks a lot, Fabian
Hi DoF Community,
I am working on a project using Universal Robots, and the customer is very worried about safety. In this case, the customer is worried about the robot having to hit someone for it to stop. So I proposed using a light curtain or an area scanner to slow down the robot when a person comes within 3 meters and have the robot stop when someone is within 1 meter of the robot. Has anyone used a light curtain or an area scanner for increased safety on a Universal Robots cell? How easily can I interface the light curtain with the robot's controller? How can I communicate with the robot when the light curtain's signal is triggered?
Thanks,
Tim