Hi @jianlan_, I opened a support ticket to help you with that. I will post my findings here afterwards.
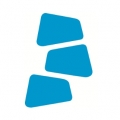
Hi Annick,Annick_Mottard said:Hello @Martin_B
I looked at your video and the drift that you experience is normal. When in ActiveDrive mode, if you stop applying a force, we don't want the robot to go in a sudden stop. We programmed the ActiveDrive so it would decelerate slowly to avoid any faults.
In order to fix the height in Z, you can use ActiveDrive's plane mode:![]()
It will force the robot to move on a plane (x-y).
What you can't see in that video (and I'm not sure how to show it), is that whenever I'm trying to pull the robot in a particular direction, it is fighting me, sometimes quite severely. To the point where it will actually pull in the opposite direction to the one I'm trying to get to.
We simply wanted to trace out a basic square, but can never get the robot to follow the path because it fights to go in another direction.
Regarding my other question; I have selected the Plane function but I am still able to move the robot in the Z axis, which is an even bigger concern at this point in time. I have a customer demo on Monday morning and I need to get this resolved before then if it is possible. Are there any other settings that can affect the locking of the Z axis?
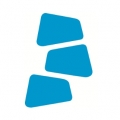
Hi David, I'm going to try and make a video tomorrow morning, showing the exact problems we are having. I think I now have a way of showing it correctly. It is mostly in the X axis, but not totally. We are also getting unexpected reactions in the Y axis.David_Levasseur said:Hello @Martin_B, Does the sensor "fight" you only in the X axis by any chance?

Thank you for the video @Martin_B, I sent you a firmware update in private. Please give it a try and let me know how it goes.

Hi @Martin_B , I wish I would have thought of that earlier but since you are now running a previous version of the firmware, it is not fully compatible with the latest URCap. The last compatible version is UCS 1.1.1. Unfortunately, this older version does not include the calibration procedure and all the new features of the latest release. The calibration has to be done like before by loading the calib_tool.urp program. The only other way around would be to send the sensor back to Robotiq for a major update. Let me know if you want to proceed with the return and I will issue a RMA number for you.
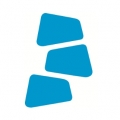
So just to be clear....David_Levasseur said:Hi @Martin_B , I wish I would have thought of that earlier but since you are now running a previous version of the firmware, it is not fully compatible with the latest URCap. The last compatible version is UCS 1.1.1. Unfortunately, this older version does not include the calibration procedure and all the new features of the latest release. The calibration has to be done like before by loading the calib_tool.urp program. The only other way around would be to send the sensor back to Robotiq for a major update. Let me know if you want to proceed with the return and I will issue a RMA number for you.
If we run the calib_tool.urp program then everything should work fine?
If that is the case, we would like to keep the unit and wait until you release a new URCap.
If, however, you think it would be better to just send the sensor back anyway, then we can do that too.
We will comply with whatever you advise is the best course of action.
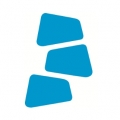
OK, thank you.
Hi everyone,
I started using FT300 with ActiveDrive URCaps several weeks ago. There two issues quite often.
I am using FT/300 + two finger 85mm gripper + UR5.
1. even when the gripper is not holding anything or in contact with objects, ActiveDrive throws out erros "excessive force is applied to the tool"
2. in the path recording mode, the robot fights against me when I try to move it, often resulting in singularity that quits force mode. Also, even I apply every little force, the robot tries to move to some singularity points.
I wonder any of you encountered this, am I expected to do additional setups before using path recording? Thank you so much!