One of our recommendations practices is to use the position_deviation_warning() method to know when you are pushing any particular move to hard. We use a threshold of 0.8. This has definitely helped make our programs more robust and limit protective stops
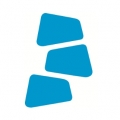
This is one aspect of it. I was leaning more towards the realm of joint health and longevity.
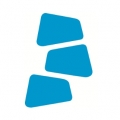
Thanks for the suggestion. it worked

@matthewd92, any idea how can we get the log in realtime? As we want to control the robot in realtime and get the warning from PC asap.
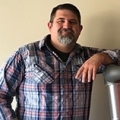
It is being streamed on port 30001, you will need to be able to decode the message packets to find the logs. There is more information on what is coming out of that port here
Using that data you would be able to get access to the log files, we do not decode that data today so not sure what you would be looking for in the message. The log files are message type 20, text message I believe. Look at the tab "3.0" for a list of all the messages that are being broadcast.
Would be interested to know if you are able to get this working.

Hi Matthew, good to know. I let my engineer intern tried and we managed to get it working. We used the "ur_modern_driver" and here is the commit for the key message unpacking. It may not be optimized and need some tweak if anyone wants to use it. But the bottom line is that it works for us.matthewd92 said:It is being streamed on port 30001, you will need to be able to decode the message packets to find the logs. There is more information on what is coming out of that port here
Using that data you would be able to get access to the log files, we do not decode that data today so not sure what you would be looking for in the message. The log files are message type 20, text message I believe. Look at the tab "3.0" for a list of all the messages that are being broadcast.
Would be interested to know if you are able to get this working.
Hi all,
In the process of tweaking the program to reduce cycle time a question arose in regard to good practice for setting accelerations and tool speeds in the program. In the interest of balancing joint longevity with cycle time what are some guidelines for determining this or a good place for me to look for reference? I appreciate your time answering my questions thank you. My installation is a UR5 with Robotic 2 finger 85 gripper.