@Tyler_Berryman
Great!
It is the most common process that customers ask. A good example to show it. You can send the example program ?.
Sometimes you should use software that generates the code as is the case of Artiminds, but the client only needs one of the functions (Spiral for example).
Thanks!
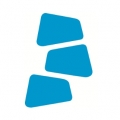
@Tyler_Berryman first of all thank you for this. It's really useful to show people what is possible with our FT300.
Furthermore there has arisen a question. We changed the skript a little bit to use this not only in a 0°-degree level. Now we can also use it to a 90° level like a wall. Our next step we want is to use it on a random level which we define by 3 points. Is there a way to force the robot to stay with the tool axis (which is the same like the z-axis of the ft300) orthogonal on the random level? And is there any longer a way to force him to make a translation along this axis of the tool?
Regards
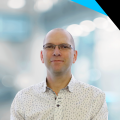
@Hammer1991
Have you tried the last template that @Tyler_Berryman has done if it does what you would like to do?
You will find it here:
Spiral search

@Hammer1991,
Thank you for the feedback regarding the Spiral Search program.
The program uses the robot's TCP position, this means that you do not have to reprogram anything as long as you position the tool in the correct orientation before calling the Spiral Search subprogram. If you position the TCP with a 90deg offset relative to the base, the spiral search will be performed in this orientation.
Louis mentioned a revised version of the program that is available on the Robotiq website. The revised version can be downloaded by clicking on the following link : http://blog.robotiq.com/spiral-search?_ga=2.123390987.1087686588.1500726322-1745763925.1494319737
In this program the template, the spiral search program is included in a script file. The included PDF document will explain how to setup the script file within a UR program.
Hi guys,
A lot of people are aware that the FT300 sensor comes with two useful URCaps functions: the active drive toolbar and the path recording feature. However, this post aims to show you guys how the sensor can also be used in a force feedback loop for insertion applications or for assembly type applications. Following the discussion I had with @matthewd92 and @lakshmip001 on how to program a spiral motion, I decided to write a subprogram to use a spiral search to find a hole.
First, I move in the Z axis to find the top of the part by using a force feedback loop with a force threshold in the Z axis. Once the threshold has been met, I call the subprogram for the Spiral Search. The spiral search is based on @matthewd92 code. To resume the spiral move, the x and y values of a pos are continuously incremented at a constant rate to create the spiral trajectory. While the robot is moving in the spiral motion, I am using a thread to monitor the force in the Z axis. Basically, as soon as the force in the Z axis falls below 2.5N, I trigger an event to stop the spiral movement. The robot then moves downward in the Z axis and releases the bearing into the hole.
This subprogram can be very useful for applications that require a precise insertion or for applications that have a vision component integrated with the cell.
Here is the video of the demonstration:
https://www.youtube.com/watch?v=PeDMZ5XjMCo
P.S. The radius and angle incrementations can be adjusted to have a finer resolution for better results!