@Sebastien most of our robots run at 90% of max speed and accel or higher. This was my experience before Hirebotics as well. We have one currently running at that rate 6 days a week, 24 hours a day and a couple more generally putting in 20 hours a day 5 days a week and we've seen no mechanical issues. They are all carrying no more than 20% of rated payload at that rate.
The thing we found with UR10's is that they need an extremely rigid base to run that fast as the robot carries a lot of momentum.
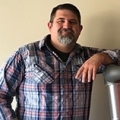
Maximum values that can be entered
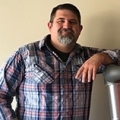
Thanks for the clarification on use @Stefan_Stubgaard that should be added to the API manual.
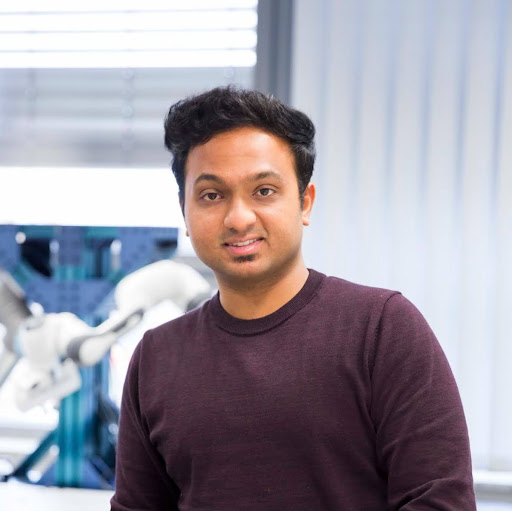
@matthewd92 and @Stefan_Stubgaard, I am facing a similar problem with the UR10 with PolyScope version 3.4. It goes into C153A4 protective stop sometimes (its very random and not very frequent and not a repeatable error). This happens when the robot picks up the 4kg part and moves towards the drop location. The motion towards the drop location involves a rotation of the wrist joint but the "Protective stop" does not happen exactly during this rotation but at random in between the waypoints. Any advise on solving this issue?
Hi pros,
We have a UR10 robot picking parts from a conveyor. Nothing fency, just a simple vacuum cup picking up a part that is not much heavy, maybe 1lbs-3lbs max.
We are adding an area sensor because when no-one is around we want to go faster with the UR. I know we can increase the speed and acceleration relatively high, like 3000mm/s for example. However I don't want to damage the robot prematurely by going to fast since the robot will fun all day. What typical speed and accelerations have you seen running for a while in your applications without running into any issue?
@Stefan_Stubgaard maybe you can provide a few comments?