Thanks @SJQ_Mirza!
@matthewd92, @Ryan_Weaver What do you guys mainly use?
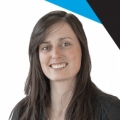
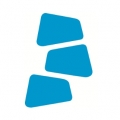
Hi Matthew ,matthewd92 said:@SJQ_Mirza the primary reason we use a lot of fiber optic sensors is we deal with a lot of aluminum parts and that fact cuts the sensing distance of inductive sensors way down as they are not as inductive as say a steel part. So we find they are more reliable and we are able to place them more out of the way of the robot and humans.
Here is an interesting article on the different types of proximity sensors with some advantages and disadvantages.
http://machinedesign.com/sensors/proximity-sensors-compared-inductive-capacitive-photoelectric-and-ultrasonic
I guess one point of clarification, are you referring to proximity of the human to the robot or sensors in the cell that help the robot to "see and sense" its work environment?
Thanks for your reply.I'm focusing on proximity of humans
Saman
I am doing research on impact of proximity based safety sensors in collaborative robots. The papers I read indicate capacitive sensors are the most common in industry. However, in service robots there is a vast variety being used. Please comment. Thanks