I posted this to the wrong board. :/
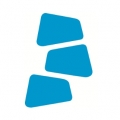
Thanks.

@mertzga Your guess is absolutely right! In the demonstration videos where the tool contacts an object and moves in another direction is utilizing the FT300 sensor's force feedback. In another DoF post (http://dof.robotiq.com/discussion/comment/945#Comment_945 ), I used the FT300 sensor to monitor the force in the x axis. I was monitoring the force on the PCB, so that the robot would stop moving the part when as soon as it was in contact with the edge of the tray. I was running a loop that was basically saying : As long as the Torque measured in the X axis is smaller than 0.5Nm keep moving in the X axis.
Loop norm(Mx)<0.5 var_1≔get_actual_tcp_pose() var_2≔pose_add(var_1,p[-0.0005,0,0,0,0,0]) var_2I was using a template that comes with the FT300 sensor to stream the data coming from the force/torque sensor. As soon as the torque in the X axis is larger than 0.5Nm, the robot will go to the next step in the program.
Yes you can increment a variable in your program everytime you place a box, so you could increment the variable "Box" everytime you place a box. Then you could use an IF statement to accomplish a certain task when "Box" is equal to . You could then use the force feedback from the sensor to place the cardboard inserts between the boxes.
If Box≟4
*Place action here: such as placing the cardboard inserts
Box≔0

@mertzga Yes, you can do this using the built-in force control of the UR.
@matthewd92 Thanks for pointing out the UR Force feature!
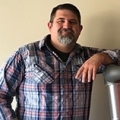
@mertzga just to further clarify what Tyler said, the ax, ay, az are given in radians. IF you have degrees you can use the built-in function d2r() to convert degrees to radiansTyler_Berryman said:@matthewd92 Thanks for answering, yes the pose is defined as p(x,y,z,ax,ay,az), where x,y and z describe the position of the TCP in meters, and ax, ay and az describe the orientation of the TCP.
I have seen videos typically of stacking type applications where the UR goes down until it contacts something then it moves upward then returns to pick an object a certain height above the point it contacted initially. My assumption is this is accomplished using torque sensing and a relative or variable way point. Where can I find some training literature that explains how to establish these types of waypoints? Can someone share some insight how this is programmed? Another question, I am using the pallet wizard to stack parts in a box, using the box feature. I need to insert a sheet of cardboard between each layer. Is there a way to insert a pause and pop-up between layers in a box sequence or do I need to do like 4 or 5 squares? Counting of some type? This is where I was thinking the touch off trick would help me I could have the robot touch off before it begins the pallet sequence then it would places the layer. Pop-up once layer is complete insert sheet. Robot again checks height and begins second layer. I hope this is a clear enough explanation.