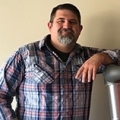
You have a typo in that linetom24 said:i tried but i have the issue to attach the screenshot
it shows me Lexer exception on line 6446: if(time>=1 & timer-1<1.5)
if(time>=1 and time<1.5):
cannot use & and your second conditional is timer-1 which if that is how you typed it is a Boolean, you want time there
the Hass send signal to the robot two times with one signal M100. the first signal stay as input to the robot for 1 second and the second will stay for 3 second . so if i need only the second signal how i can use the timer. i tested may times but it is not work. i appreciated for the help
for instance i use like this before start
time=0
timer=false
main program
if DIO =true and time=1 sec
timer=false
else DIO=true and timer =3 sec