What do you guys use @gradyturner86 @AlexYust @dhenderson ?


@Kaleb_Rodes would you be comfortable to share some pictures and CADs? Looks like a great idea!
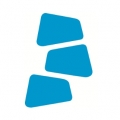
@Samuel_Bouchard Sorry but we can not share any pictures or CAD drawings at the moment, because we're still in the prototyping phase. Once we complete our final design I will be happy to share with everyone!Samuel_Bouchard said:@Kaleb_Rodes would you be comfortable to share some pictures and CADs? Looks like a great idea!
@matthewd92 I have used a soft piece of foam in the conduit to control the amount of cable slack during an application. The foam keeps the cables from retracting.

@matthewd92 we don't have plans to modify that in the near term. It's not perfect I agree, but we hope that this issue will be solved in another way in the future. Thanks for the feedback.
@Kaleb_Rodes thanks, looking forward to seeing your design!
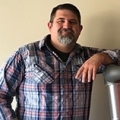
@AlexYust are the brackets mounting it to the arm custom, or are those IGUS standard brackets?
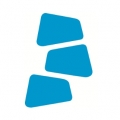
@matthewd92 The clamps and cable carrier are all from IGUS. See the following link for additional information:
http://www.igus.com/wpck/14869/N15_01_27_UR_schellen?C=US&L=en
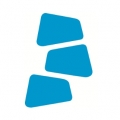
matthewd92 said:@RobBauer that is very similar to what we are doing but we have not been using any printed brackets. We have some industrial velcro that has a 3M adhesive backing that we stick to the arm and then we use a velcro wrap that sticks to that and wraps the cables. It works pretty well as the velcro no longer moves up and down the arm as it's done in the past. I like your idea and it's very similar to the design that has been rolling around inside my head. One question though, what is the bracket that has the tennis ball on it?
Mathew, our environment makes something like the 3M adhesive solution a little doubtful, though if the Velcro attached to the arm also wraps completely around it and laps itself, it might hold up well enough.
For our worst case installation, the robot is located inside the machine enclosure and had to be put in a protective suit. The original was actually a large Tychem coverall (~$14 USD), using Velcro One-Wrap to bind the suit closer to the arm. The Velcro held up well, through several suits, while the suits usually lasted over a month before needing replacement. We have a better cover now, designed for the UR-10, but it still required extra Velcro strapping.
The bracket with the tennis ball was for a demo where two robots pass the ball between each other, one picking it up, the other putting it back down in the bracket/holder. My boss made the suggestion one morning, and I had the holder designed and printed, and the robots programmed, all in a couple of hours. The robots talk to each other via Modbus. I had T-Slot tracks inset into the work bench to make quick and secure setups very simple, with plastic filler strips to cover the open slots most of the time.
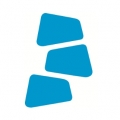
@abeachy_HG24 yes sure. We print our company name on it as well so my guys could make a custom version for you. The wire covering is just standard wire wrapping but makes it look much better. I can add it if you can't get it on your side, no problem as well.
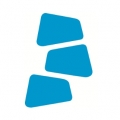
@gerenga What would be looking as far as cost?
curious what everyone is using for cable management up the UR arm. We try to use soft systems such as Velcro to limit the possibility that the cables get cut or we create a new pinch point. As opposed to other manufacturers which route air and power through the arm we find cable management much more of a challenge with UR.