As clarification I know how to figure this out based on the stopping time of the UR5 however I have only found information for when the robot is moving with max payload at full reach. For example at 1.5 m/s the stopping time is 500ms. I would like to find stopping time of the robot at half of its reach with a 2kg payload (for example).
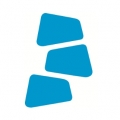
Dear AZalmanov,
Please note that ISO 13855 is generally intended for more-or-less stationary hazards, to which you can define an approach speed that then refers to the (walking) speed of the human operator.
In the case of risk reduction by "speed and separation monitoring" (as described in ISO 10218-1, -2 and in some detail in ISO/TS 15066) the speed at which the operator and the hazard - i.e. the moving robot - approach one another is composed of contributions from the motion of both. Perhaps you have already looked at ISO/TS 15066 "Collaborative robots", which gives a more detailed discussion. The protection objective is to make it impossible for the operator to reach the robot while it still moves.
The criterion for tripping the condition is that the actual separation distance S drops below the protective separation distance S_p. That is:
S < S_p to trigger the safety reaction, e.g. stopping the robot.
Let me at least quote the formula for the "protective separation distance" from the TS:
S_p = S_h + S_r + S_s + C + Z_d + Z_r
The quantities are:
S_p = protective separation distance
S_h = approach distance covered by the human during latency of sensing system (measuring distance to operator), during controller reaction (processing time before deceleration of the robot begins), and during the stopping time of the robot
S_r = approach distance covered by the robot (moving part closest to operator) during the latency of sensing and controller reaction
S_s = stopping distance of robot (moving part closest to operator)
C = "intrusion distance" as also defined in ISO 13855, i.e. the distance that a part of the body can intrude into the sensing field before it is detected
Z_d = position uncertainty on measured distance to operator
Z_r = position uncertainty of the robot system (in my opinion, this can be neglected for modern industrial robots)
The suppliers of industrial robots must provide data on the stopping behavior of their robots, at least on a very coarse, worst case level. Sometimes at this level of simplification, a "linear" model of a constant deceleration can produce reasonable results. But, as you've stated that the worst case approximation is not suitable for your application, the question becomes more difficult.
In my view, you have one realistic option, namely to define a set of representative measurement conditions and measure the robot's stopping behavior in your application. The idealistic option is a research project to develop a safety-rated online computation of the stopping distance that applies to the instantaneous conditions of the application (robot pose, joint speeds, accelerations, payload). Suppliers should be interested in pursuing this topic.
Knowing that your post is nearly a year old, I hope you've already found a good solution!
Best wishes.
During calculations using minimum Distance formulas from ISO 13855 I have ran into a question as to what exactly the variable Vs is when calculating Ss (contribution to the stopping distance from the robots stopping distance). Vs is a function dependent on time of the robots deceleration. Where could I find the robots maximum deceleration for this. Also if anyone can provide a sample calculation of this that would be much appreciated. I have calculated this as a worst case scenario but am not happy with the separation distance, therefore I now need to consider the actual scenario.