@akihikoy what kind of frequency would the "continuous finger control" need ?
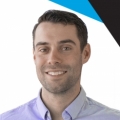
@akihikoy 200Hz is the maximum you can obtain if you do direct Modbus RTU communication, the USB converter most probably slow this down.
Also, controlling the Gripper at such speed will most probably give you a weird behavior. The Gripper is developped so that you send close / open / move commands and wait for a feedback. Non-stop movement command at this pace will probably gives you a shaky movement.
First thing you should do is have a PID loop that dampens the movement you are doing. Know that the motion as an acceleration ramp. So if you always ask for very small movement you will never reach the cruising speed (the speed we spec is for a full stroke), thus your slow motion. For example, we usually recommend to have at least 2.4 mm of clearance on a part to get that speed up so that the object detection works. Smaller movement then this = gripper still accelerating and no object feedback & bad force control.
Also know that the Gripper has an embedded function similar to what you are doing. The Gripper has a "re-grasp" function were it will detect if parts are slipping out by applying on continuous small pressure. When it detects the parts are slipping (fingers are closing or opening on it) it automatically moves. That function is turned off if you use force setting to 0. That function could probably be in conflict with what you are doing.
Many thanks!