@Bryan that should be possible. What would the path between the points look like?
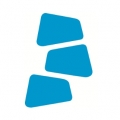
@David_Gariepy I found this description online (http://www.zacobria.com/universal-robots-knowledge-base-tech-support-forum-hints-tips/knowledge-base/planes-and-position-variables-1/) and I think that this is approximately the solution you are suggesting. I was wondering do I have to create 1 reference plane with “fixed” waypoints and than another 2nd plane where I reteach the 3 plane points (for other product positions) so that the waypoints change accordingly to the plane refernce?
I was also wondering how time consuming is it to reteach this plane feature (approx.)? Because the cleaning of some parts can take up to 80 minutes, so for example when this reteaching takes me 5 minutes I still achieve 75 minutes profit.
I totally agree with your second remark, the precision is relative to these 3 points and I should explore if this a problem for the process. I also will look into custom fixtures.
@matthewd92 Unfortunately all holes have a different size, otherwise vision would be a good solution.
Hi pro’s,
For productcontrol our products are cleaned manually by an operator at specific product points/locations. We produce a lot of different products and they are all analyzed in the same installation. When a product is analyzed, a totally different product will be analyzed next. Because of this continuous product variation an universal product fixture for positioning the products on exactly the same manner is almost impossible. That is why the product is always positioned in a different way. During this project I am trying to figure out what the possibilities are to automate this proces.
Therefore my question is:
Is it possible to create a path between two or three productspecific reference points. For example: the operator positions the robotarm (with a positioningtool) against a productspecific start- and endpoint. Because of these two reference points the position of the product can be determined and a standard programmed path will performed between these points?
Thanks in advance,
Bryan