@abeachy_HG24 the short answer is Yep! So now for a bit longer answer...
There are a couple of ways to do this but all revolve around the same premise. If you were to wrap the entire program on the second robot in an if statement you could then monitor something on the robot and only execute the program if that condition were met. You would use the "Check expression Continuously" feature on the if statement, little check box.
Now how to get them to communicate with each other could be done using digital I/O from one to the other, you would need to use a relay to isolate the 24V sources properly. Another option is to put them on the same network and then use a general purpose modbus register to communicate with each other. Modbus registers 128-255 are reserved for general purpose 16 bit use. The master could set the modbus register to some value, say 100 when everything is good and the second robot can do its operations and then 999 when its time to stop operation and return home.
On the master robot you would use a bit of URScript to write a value to the modbus register using something like this:
write_port_register(128, 100) # this would set the value of the register to 100
or
write_port_register(128, 999) # this would set the value of the register to 999
On the slave robot you would set-up a modbus client that connects to the master robot using the master robot's IP address.
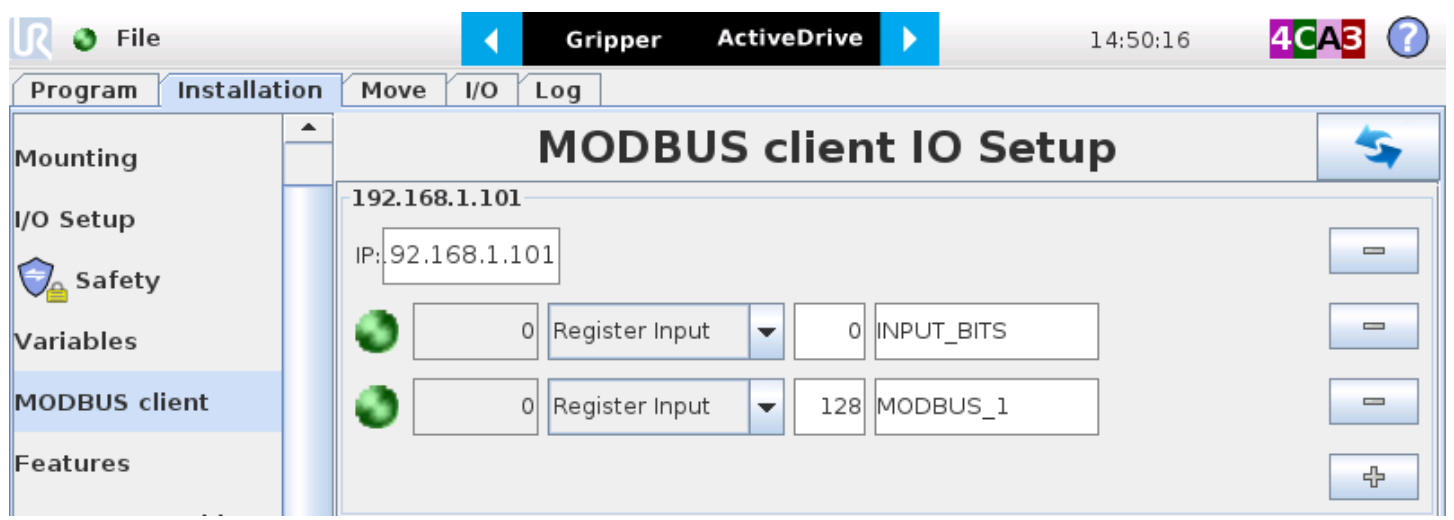
The code on the slave robot would look something like this:
if MODBUS_1 != 999. #Make sure the check box is checked for checking expression continuously
...do your tasks here
end
stopj() #This makes sure that if the robot was moving that it stops
Your homing routine would go here, you may need to define the path to get home based on what it was doing at the time
There is information here on using the modbus registers, the nice thing about going this route is there is no physical wiring between the robots.
@Ryan_Weaver did a great write-up on using the modbus to mirror movement between two robots and there is good information in his white paper on how to connect the two robots together using the modbus.
Let me know if you need more information.
Is there a way to have some sort of logic to essentially interrupt the robot's current task and have it go home?
We have two robots that are working on the same part, the first robot performs a couple tasks to it and then moves clear so that the second robot can perform a task, and then once the second robot is done they both go home and that operation is complete. The issue we are seeing is that if something goes wrong with either robot while it is performing its task, like the pressing operation not completing its cycle correctly, that part needs to be rejected. The first robot is the one receiving feedback from the press so if it doesn't complete it knows to reject it, but the second robot doesn't and will continue its program until it finishes the task, which is not desirable because we don't want to continue doing work to the part if it has been rejected.
So we were thinking we might be able to potentially just have something that basically interrupts the robot and tells it to go home and get ready for the next part. Is this possible with the URs?