@usman379 Welcome to the forum, I hope that you find many useful resources here.
I think that this job could be automated using the UR5 and (2) Robotiq 2F-140 grippers, those are the 2 finger, 140mm opening grippers. This would allow you to control the width of the log by going to various opening positions and slicing off the proper number of sheets similar to what the human is doing. you may need to create some customer finger tips that are thin but wide to more easily slice into the stack without damaging the sheets as well as provide more support by providing a wider area to grasp.
One issue that I see right away is handling the loose sheet after the log is rolled over. This could be tricky to handle with the robot due to lack of "eyes", would it be acceptable if that sheet did not get placed on top, could there be another way to automate that action such as an air blast that flips the loose folded sheet back on top?
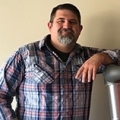
@Catherine_Bernier can someone from there reach out to Usman regarding distribution in Pakistan?usman379 said:
Robotiq, does not reply via their website and I tried the phone and the dialed "4 for sales" but got the answering machine in french, . I have been trying to get a quote from Robotiq for 2 weeks now. any ideas or contacts (email/ phone number I can try)
thanks a lot
Cheers
Regarding the movement of the tissue, is the tissue always moving at the same speed? I would think the best way to do this would be with an encoder that is monitoring the motion of the tissue. UR has some built-in functionality for conveyor tracking, using encoders to get speed information from the conveyor, you could probably use this functionality to do what you need if the conveyor speed varies.
I personally wouldn't try to use vision to solve that issue, I think it would be a very difficult challenge to try to find the light for pickup as humans we are easily able to see that light and track the motion in real-time. Sensors would probably be a better bet.

@usman379 I apologize for the long delay getting back to you. I will look into the problem since I am not certain why you were not contacted from one of our application engineers. I have also sent you an email so we can discuss pricing in a private conversation.
I agree with @matthewd92, I think that the use of two robots would be best for lifting a "Tissue Log" of this length. Since the operator is using both of his hands to manipulate the log, I think the easiest way to automate this task would be to use two robots to recreate his actions. I would also recommend using custom fingertips on the gripper to make it easier to pick up this stack of tissues. Something like this could be a good fit : http://dof.robotiq.com/discussion/comment/1239#Comment_1239.
The 2F140 gripper weighs 1Kg, so if you add the 3Kg associated to the "Tissue Log" you would have no problem using 2 UR5 robots for this application. The 2F140 gripper also comes with a software package that makes it very easy to program the gripper through the Teach Pendant (Robot's Touch Screen). This also makes all the programming centralized on the teach pendant. Here is a video demonstrating the programming of the 2F140 gripper through the UR's teach pendant : http://fast.wistia.net/embed/iframe/apqy723265.
Just an idea, but a small linear actuator could be used to separate the right amount of tissues to be moved from the conveyor. It could positioned on a rail to be adjustable to various amounts/thicknesses of tissues.
Dear DOF Community,
This is my first post. I am a Mechatronics (Industrial Automation and Robotics) engineer from Pakistan. For almost all of my career I have been working in the Industrial automation (PLC/ DCS/ SCADA/ HMI/ Historian/ SIS/ F&G/ Instrumentation) Design, Management, Commissioning and maintenance based roles. Now I am getting a chance to work on robotics related Projects too, and I am very impressed with the Universal Robotics and Robotiq products.
here is my question
We have a customer requirement regarding the robot.
The maximum pay load for the robot is 4 kg (excluding the gripper assembly) and maximum reach is 90 cm.
The robot has to
1. identify a certain width of a tissue log with a specific number of tissue sheets
2. pick up the tissue log
3. rotate the log through 90 Degrees
4. then put the log on to a conveyor belt near by
The Height of the tissue log is 10 cm.
The Length of the tissue log is 150 cm.
The Width of the tissue log is 2 cm to 10 cm.
The maximum weight of the tissue log is 3 kg.
But the width and weight may vary job to job depending upon the number of sheets in the job.
The width of tissue log and number of sheets may vary job to job.
The pictures and video clip of the machine when a human is doing the same job as the robot would have to, is attached.
We have selected UR family robot of Universal Robots for our current application.
Now we are required an end effect-or that is connected to UR family robots and do the job as shown in the video (picking up the log, rotating the log through 90o and then place the log on to a conveyor belt)
Please suggest an end effect-or and also confirm its compatibility with UR robots.
Also please suggest that our current application can be handled with single robot and single end effect or or we have to move to two robots with two end effect-or.
We are selecting two UR5 Universal Robots and 2 Robotiq 2-FINGER 140 grippers for this application, and we need the advice and comment of the experts at DOF community to finalize our selection. Will Vision or camera be required.
Here are some attachments on Google Dirve
List of files on the Google Dirve link
InterFolder Machine 3D Animation
Machine Picture (1)
Machine Picture (2)
Machine Picture (3)
Machine Picture (4)
Machine Working Vedio_mpeg4
Scope_Auto_Separation_jinsung
tissue log
https://drive.google.com/drive/folders/0BwQl_IVppyQGRmUyZFV5RWZWOUk?usp=sharing
Thanks a lot for sharing your insights
Thanks and Regards,
Muhammad Usman Younis
Engineering Manager,
Devrim Technologies Pvt. Ltd.
(Subsidiary of Power Solutions Pakistan)
Head Office:
48-G III Johar Town, Lahore-Pakistan.
Tel: +92-42-3529 0781 - 82
Fax: +92-42-3529 0780
E-mail: info@powersolutionspk.com
Usman.younis@Devrimtechs.com
Cell: +92-331-5422355
https://pk.linkedin.com/in/usmanyounismaashaaallah