@abeachy_HG24 I'd love to say I've never seen this but I have. It usually plagues us on projects where we are pushing them to the limit. I agree with UR about the acceleration. One of the things I wish we could do is define separate accel and decel values but we can't. Have you tried blending the moves? You may also want to put two waypoints with a blend so that one can be the accel and one the decel allowing you to slow down over a longer period.
Another thing to check is that your TCP weights and center of gravity are set correctly. Have you weighed the total payload accurately? This becomes more critical as you start using the full length of the arm.
Where re are you seeing the protective stops? Does it generally happen at a point that is an end point, meaning the robot is stopping there?
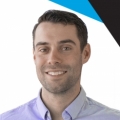
@abeachy_HG24 if you push the robot speed it's usually quite important to have the proper TCP with the correct CoG like @matthewd92 said . Once you get that, you will need a dynamic payload adjustment.
In your program, you should set the payload to whatever you have, also set it when you have nothing picked. That will help you a lot if you want to speed up and avoid those. I'd say if you pick anything over 100 g you should adjust your payload.
We just updated the tables for mass and CoG. We will add something for the TCP shortly, otherwise you can approximate from the Gripper tech drawings.
Hi pros,
I am working with some UR 10s and we are experiencing what seems to be like completely random protective stops. I will run a program 7 or 8 times flawlessly and then I will run it again without changing anything and I will get a protective stop. I've talked to UR and they suggested reducing the acceleration but 20% each time it happens. They are thinking we might be running it right on the borderline for protective stops so that is why it's only every once in a while. That concerns me a little because there's no way to know if we are right on the border besides running the program many times, and we are on a crunch for time. Has anyone else seen this happen? Also, any tips on how we can avoid this? We could slow it down, but we are pushing it because of cycle time.