Thanks David for this great question!
@matthewd92, @Nicolas_Lauzier what do you think?
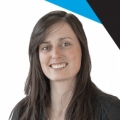
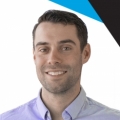
@david_firam for your initial positioning you should use 2 holes on the floor and have your mobile plateform.
Here is an example of mobile platform done by Faude, one of our partner in Germany, they sell this as a standard cell. It's on wheels to move it around but then the handle on the side will fix it and the 2 rods you see on the bottom will align it infront of the CNC machine. They sell this standard machine tending cell with our Gripper on it by default with optional FT Sensor and Wrist Camera. They are not the only distributor doing that, I'm sure @Catherine_Bernier could help you find someone doing that in your area!
Hello,
I am currently working on an application to pick and place some parts using the UR10 robot. Our robot is installed on a mobile platform that can be manually moved making it ideal to take the robot out of the production line in case something unexpected happens.
My goal is to use the FT300 in combination with a custom gripper to palpate the machine so I can offset the robots waypoints in case the robot was moved from it's previous position (not much, just a couple of mm). Our application requires the robot to pick and place parts on centering pins so accuracy is a must.
I was wondering if the FT300 sensor is feasible for accomplishing such a task.
Thank you