@luke_savage How did you deal with this in your application? I was also wondering how many waypoints you got programmed in your program.
https://www.youtube.com/watch?v=DfkcvX-qDRA
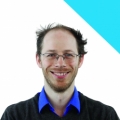
From the How-to of UR web site I found an example that show how to modify the speed slider from inside a robot program :
http://www.universal-robots.com/how-tos-and-faqs/how-to/ur-how-tos/setting-the-speed-slider-from-a-program-15293/
I modified the Robotiq force sensor template program to set the speed slider based on the force (see Thread_2 on picture)
I filtered the speed parameter with a moving average to obtain something smooth and try this with a trajectory recorded with the Path node.
This program executes the recorded Path with a speed that decreases when the force increases. It could be useful in deburring task to reduce speed accordingly to cutting force.
Someone could use a similar speed slider hack to adjust the speed at contact point of a fixed deburring tool, for example using the distance between robot flange and tool as parameter.
Hi Pros!
I have been working on a certain application and I wanted to get some advice from you. The application is a deburing application where the deburing tool is fixed and the robot is holding the part. Below is a video of the application with a dummy part that I used to illustrate the issue that I have. The problem that I have is that I want to have the relative speed between the deburing tool and the surface of the part to be constant. So basically I would need the TCP position to update continuously to always be at the point of contact between the part and the object. Otherwise, when the robot tool changes directions I get speed variations on the trajectory. Since the part that I have is not on a straight line, I use the path recording option with the Robotiq FT sensor in constant speed mode to record the trajectory. So off course programming various waypoints with the proper speed would do it but this is long, considering that the clients has many parts to program. Do you have any advice how I could do this?
https://youtu.be/Yq_2TaR7nnQ