@matthewd92
That's funny. I was just looking at this system this morning and referred their video to a client. I did work on some vibration feeder in the past were we actually designed the entire system. So basically buying a vibration motor on Mcmaster Carr and designing the whole thing. Turns out that we spent quite a lot of time just figuring out the proper vibration parameters, weight balance and feeder design to make good part separation on the table. I took a look at the Graco G-FLEX manual and you have a lot of parameters to play with. Which is good because you need this to adjust to the different parts that you want to process. I have not worked with this systems but it looks good based on what I am expecting from such a system. It would be a great combination with UR and Robotiq camera! If someone is able to try it out it would be nice to have feedback and videos here!
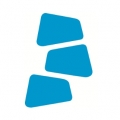
matthewd92 So, It means I can use Asrily feeder with the Robotiq Wrist Camera. But Asrily feeder vibration can only be obtained when object is not detected and the other features of Camera cannot be controlled. And as the Robotiq camera takes minimum 10-20 secs to detect an object process is slow. And Robotiq camera can detect only one object per cycle.
https://www.youtube.com/watch?v=ZhbgumR4W74&feature=youtu.be
As shown in the video can Robot pick randomly placed screws on the flat surface??
So, UR camera can work this feeder. Am I right with the conclusion.
Thanking you in advance.
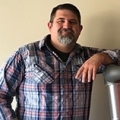
From their specifications the largest part is a 3"x3"x1.5" with a maximum of 30 pounds on the tablemertzga said:What is the largest part dimensions the Graco feeder can process?
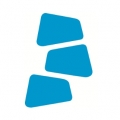
For those looking for Flex Feeders compatible with larger & heavier parts such as those you described Matt: Asyril is preparing to release a new, larger feeder in June 2017 - using the same 3-axis vibration technology known from our smaller vibrating platforms. Feel free to contact me for more info...
The following link shows an integration example showing the Asycube 240 platform featuring a Universal Robot and a wrist-mounted camera similar to Robotiq's:
https://www.youtube.com/watch?v=yetFv3f1wTE
Anyone using the Graco flex feeder? We are looking at using this for one of our customers due to the flexibility of being able to redeploy it easily versus purchasing a hard tooled vibratory bowl feeder but would like to speak to someone that has used them. Are there other brands that we should be looking at instead? The current part we are feeding is roughly 3" long and about 1/2" OD but its cam shaped. We plan to use the vision from the feeder to also locate a feature on the part once we pick it so that we know precisely how to place it onto the fixture the part is being loaded onto.