For approach 2 you could send position data via robot modbus tcp registers. Several way to send data exist, socket connection, ...
I am not sure to understand the issue with approach one.
Are you using robotiq wrist camera ? If yes, you could contact our coach team for some advice: coach@robotiq.com
Background:
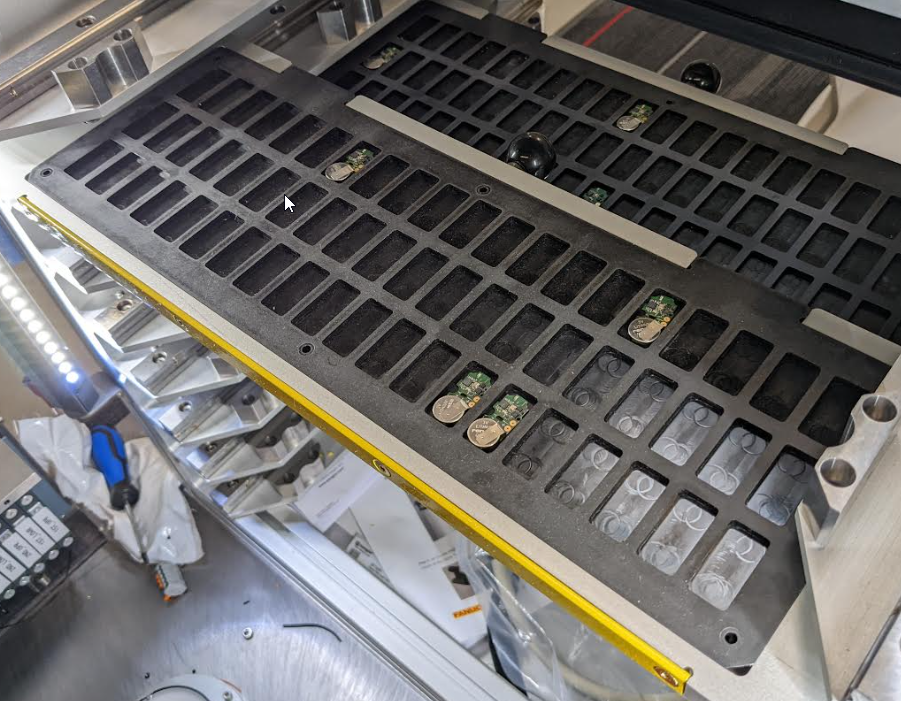
Pick PCBA to program and then put back to the original location
UR5 / Allen Bradley PLC
Sequence:
1. Vision system detects the present/absent of PCBA on a tray (3X20)
2. UR5 pick up one PCBA
3. Scan barcode on the 2nd Keyence camera.
4. The 2nd Keyence camera will also tell UR5 the amount of distance offset of the programming contact points
5. UR5 will move the PCBA to a programming station (10 total) preciously for program
6. After PCBA programming is done, UR5 pick the PCBA from programming station back to the tray
Questions:
Approach 1. Try to use palletization in UR, but it need to run all tray 3X20 location. Is there anyway that I can make the UR to do the 5th of 60 movement.
Approach 2. If I am not using palletization, I want to use PLC to calculate the robot pose, but how can I send over?