To make an integration on a non supported robot you need to know the following technical details:
- Tool mechanical connection
- Tool electrical connection
- Tool control capability
1/ Tool mechanical connection
There are different type of tool mechanical connection on the market.
Here are some examples with a 6 axis arm and a scara robot:
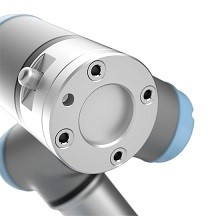

The left type of flange is the most common and robotiq have some on the shelf accessories to perform mechanical connection. Mounting on other type of flange like the above scara robot example may be possible with an adaptive plate (example of adapter for scara robot: https://epson.com/Accessories/Robot-Accessories/Tool-Adapter---%28for-G3%2C-LS3%2C-T3%2C-RS3-and-RS4-Robots%29/p/R12NZ90035).
We will but the focus on the most common type of flange ( the left one).
Here are the different elements with describes the tool mechanical connection:
- PCD (Pitch Circle Diameter)
- Threaded hole size
- Number of threaded holes
- Centering diameter and tolerance
- Centering height
- Pin diameter and tolerance
- Flange diameter

The centering part of the flange is made to center the tool on the flange.
The pin is made to fix the orientation of the tool.
here below is an example of flange:

2/ Electrical connection
The electrical connection includes:
- Communication lines
- Power lines
3/ Tool control capability
The control of the tool is done using:
- a communication protocol
- a software
- Modbus RTU (Robotiq default communication protocol)
- EtherCAT
- Ethernet/IP
- Modbus TCP
- ProfiNET
- CANopen
- DeviceNet
You can find communication protocol available on the robot by checking its documentation.
Then come the software part to communicate using those protocol. Check how to use those protocol on the software side. The software complexity may vary from one robot to another. In some case you may have to write some piece of software.
Now that we know robot specification, in the next post we will see how to list the necessary equipment to integrate a Robotiq gripper.
I would like to share with you some guidance about how to integrate a Robotiq device (ex: 2F, hande, epick or airpick) on a robot.
Keep in mind that the reference and updated information for information remain device manual.
First let's have a look to type of robot on which you may want to make an integration. The amount of work needed to make an integration will change depending on the robot.
I see 3 categories of robots:
1/ Plug & Play robots supported by robotiq
If you have no robotique integration experience choice the easy way, use a plug & play robot for which integration is supported by Robotiq.
For those robots Robotiq provide all you need to seamlessly integrate on the robot: hardware (coupling, cables,...), software and documentation.
At the time of this articles plug & play robots are (Please check robotiq support page for latest information https://robotiq.com/support):
- Universal Robot (All products)
- Techman Robot (hande, 2F, ePick, airPick, FT300-S)
- Omron Techman robot (hande, 2F, ePick, airPick, FT300-S)
- Doosan (hande, 2F)
- Aubo (hande, 2F)
- Hanwha (hande, 2F)
Using a plug&play robot remove the integration challenge. Anyone can make it in few minutes !Robotiq sells hardware kits for those supported robots so no need to scratch your head to know what you need. Your local distributor will be able to provide you those kits.
2/ Plug & Play robots supported by robot makers
Some other robot makers provide documentation and software for plug&play integration. Hardware is selected among robotiq accessories.
Those solution are directly supported by robot makers.
Here below are few example:
- Kinova
- Kassow
3/ Non supported robotsThere is always a way to integrate robotiq gripper on a robot but you have to be skilled on how to integrate Modbus RTU device. It should be not problem for an integrator but challenging for a person who have no integration experience.
In this category are especially industrial robots.
On the next post will an overview about the robot information you need to know before starting integration.