hi, bcastets,
I'm using the jaka robot, and try to control a gripper via the Modbus RTU. I already connected the voltage and the 485 +/- on the mini cab(masterBus_RS485), but on the app side, i am confused with the configuration. The 'register addr' and the 'number' should match the gripper protocol config right?
Thank you for your time!
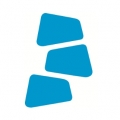
@bcastets
thank you, i will ask them.
I open a discussion so that people can share their integration experience on Jaka.
At the time of this article I don't have the perfect method to make such integration.
I see 2 potential methods:
1/Integration via Modbus RTU
This integration would required the following hardware:
Here below are what should be the step to setup Modbus RTU communication.
On the controller side the physical connection should be something like this:
On the program side it looks possible to send modbus output and get modbus input.
To check if the communication work you can try to write 2304 in the modbus digital output AO1. This will turn rATC to 1 which will activate the gripper and turn rGTO to 1 which will move the gripper to the requested position.
Register 1000 (composed of 2 bytes):
Then to move the gripper you can write the requested position in the range 0-255 in AO2.
- AO2 - 00000000(Byte3-Position request)00000000(Byte4)
AO3 can be use to control speed and force.2/IO coupling
On latest IREX trade show in Tokyo, IDEC display Jaka robot with a 2F85 integrated with Robotiq IO coupling.
It was working well but IDEC had to make some electronics to adjust the type of IO (NPN/PNP) so that IO coupling and Jaka IO match. Connector and pinout also had to be adjusted.
Here below is Jaka tool IO (connector illustration is from tool side):
Robotiq have 2 IO coupling. One for TM and one for UR.
Here below are the IO type for those robots.
TM robot tool IO:
Doosan robot tool IO:
- Digital input are PNP
- Digital output PNP
It looks like the TM IO coupling is the best fit for this integration. Here below is the pin out of this coupling.It looks like some wiring is necessary to match the pin out.
Please share you integration experience with us.!