@renaldi
It is not possible to adjust the speed on each waypoint of multipoint path. Speed can only be set on multipoint path node.
You could eventually use several successive multipoint path and change the speed on each of them.
If you want to split your current multipoint path while keeping your waypoints, you can make a copy of your current multipoint path node and delete waypoints you don't need.
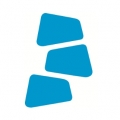
bcastets said:@renaldi
It is not possible to adjust the speed on each waypoint of multipoint path. Speed can only be set on multipoint path node.
You could eventually use several successive multipoint path and change the speed on each of them.
If you want to split your current multipoint path while keeping your waypoints, you can make a copy of your current multipoint path node and delete waypoints you don't need.
Question. Can i insert a new Multipoint path after my last waypoint and still keep the zero force / force control on the new multipath with the new speed? or how do i program this?
thanks for your reply
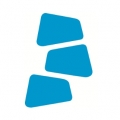
Thank you for your reply.bcastets said:@renaldi
Just add the next multipoint path after the previous one. You don't need to make sensor zero again. The zero is done only one time before entrering the force control node.
i am sanding in 45 degree angle going into a plus 45 degree angle. so the arm is stretch out quite a bit. i noticed when i run my path force control have a some what stable pressure on the surface, but there is some points it doesn't have near the 20N i will try make a video of these points where i see the pressure falls.
Is there positions on the robot it cannot apply the correct force on the tool side?
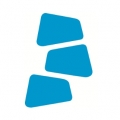
I was thinking the same. ill make a video and you can feedback your thoughts and ideas ill try upload the video later today...bcastets said:I would say that it is better to avoid position where the robot arm is fully extended.
Strong momentum makes things harder for the robot.The robot itself is also more likely to bend.
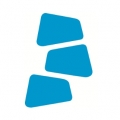
i noticed there are places where it almost dont touch the part and it not even close to deliver the 20N on tool head.renaldi said:I was thinking the same. ill make a video and you can feedback your thoughts and ideas ill try upload the video later today...bcastets said:I would say that it is better to avoid position where the robot arm is fully extended.
Strong momentum makes things harder for the robot.The robot itself is also more likely to bend.
is there a way to adjust the joints so it runs more smooth it jumps alot on my surface mostly because of the robot joints.
or does anyone have any tip or tricks for this type of part sanding?
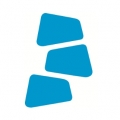
Thanks for your input i appreciate all your help. i will try move it close to the base of the robot. and see the result. now since i have made my entire program in multipoint path. Is there a way to use the same program? in my mind the way points are fixed to the coordinates. if yes can you give me an example to program it?bcastets said:@renaldi
I think you should see some improvement if you have the part closer to the base of the robot.
Also could you check the displacement limit on the force control node ? I am wondering if the limit could eventually prevent the robot from moving to the surface.
As fare a I know there is no possible adjustment of the joints to improve force control application.
Renaldi
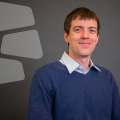
@renaldi
It is possible to translate the trajectory to a new location by by converting your trajectory in relative trajectory.
I working on an article to explain how to do that. I should be completed a the beginning of next week:
https://dof.robotiq.com/discussion/2335/how-to-convert-base-frame-trajectory-into-a-relative-trajectory/p1?new=1
Dear experts. i have made a long complex program using only multipoint path with force control, my question is can i control speed between set points?
i have issues with when the robot arm have to move more than 45 degrees it tend to jump on my surface and would like to slow it down at those areas.
how can i solve that? please write examples...
UR10 CB3
COPILOT
URCAP VERSION 1.14.5.5896
POLYSCOPE VERSION 3.14.1.1031110
thanks....