Hello @11011001
In the Force Control node, Did you try using the current position parameter as shown below (green arrow).
This means it will always use the current position to apply the force. The path in the force orientation won't matter.
Targeted position means that the path in the force orientation matters. It will affect the force applied. It is mainly use when you path is clearly defined which is not your case.
Give it a try and let me know how it goes.
Other suggestion, We can use the "Contact Offset" feature at the beginning of a run to touch the wheel and then know how worn out the wheel is and adjust the trajectory accordingly.
Let me know if you want further details.
Regards.
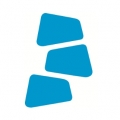
In regards to the Targeted vs Current, I just tried that and the main thing I noticed is now the part is not reaching the wheel at all. So to give context before the Force Control (with a Multi-Point path inside it) I have a "ready position" that lines the part up with the wheel but is not super close to it. When I had it on Targeted it moved into the wheel. Do I need to adjust that position closer for Current to work? If so how close does it need to be?MarcAntoine_Gauthier said:Hello @11011001
In the Force Control node, Did you try using the current position parameter as shown below (green arrow).
This means it will always use the current position to apply the force. The path in the force orientation won't matter.
Targeted position means that the path in the force orientation matters. It will affect the force applied. It is mainly use when you path is clearly defined which is not your case.
Give it a try and let me know how it goes.
Other suggestion, We can use the "Contact Offset" feature at the beginning of a run to touch the wheel and then know how worn out the wheel is and adjust the trajectory accordingly.
Let me know if you want further details.
Regards.
Thank you for your help.
I am using a UR5e with the Robotiq Force Copilot. I am doing a deburring program and I have an asymmetrical part that the robot is holding and using a force control and Multi-point path to run the 3 unique sides against the deburr wheel at 4Ns of force.
The strange thing I am seeing is it seems to be pressing decently for the first side, but the second side is hardly touching the wheel, and the third side is better than the second but less than the first.
I found that changing the positioning of the path on those two sides might resolve this, but I am confused because I was under the impression that the force control would override the positional location of the path until it hit the 4N (or whatever it is set to). Am I mistaken in this understanding?
I suppose my concern is as the deburr wheel wears down is my program going to cease to be effective?
Since the location adjustment has fixed my issue this is more about understanding why than fixing the problem, and a bit of covering myself for future problems (wheel wearing down).
Thanks!