Do they want to use UR for removing the flash of casted parts?
In my case, have experience to use UR for deburring of casted parts.
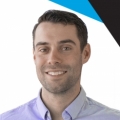
@NicoHanstein great! Yes please tell me when you are more advanced, you can also ask me if you got any questions on the FT-Sensor use.

Hi @NicoHanstein is it possible to share the video directly here with some information on the hardware used?
A customer wants to do deflashing of casted parts. Has anybody done that with the UR? If so, how?