Hi erin_thomas,
What is it you need to do? The UR3 robot comes with a control unit that has lots of digital inputs and outputs, as well as some analog inputs and outputs.
Regards.
Paul
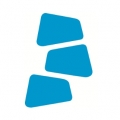
Well, have you taken a look at https://www.universal-robots.com/academy/? There’s plenty of ressources there to help understand how to program the UR robot’s input/output. Especially, take a look at the fifth training for the E-Series, it is focused on interfacing with external machines.
Regards.
Paul
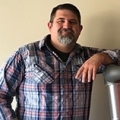
You can also get a URCap from Universal Robots for screw driving by upgrading to version 5.4 or later. Go to the installation tab, under the General category on the left hand side, the last entry is screw driving. Here you can setup which outputs and inputs you want to use to control the screw driver as well as which TCP setting defines the end of the screw gun. Then when you are writing the program, under the advanced tab is a screw driving section where you can define what you are trying to do with the screw driver. Hopefully this helps to simplify what you are trying to do.
Check out this manual, pages 18-23, and you will see that a lot of those inputs and outputs correspond directly to the selections that you make on the installation tab for screw driving.
We recently purchased a UR3 robot and Kolver Pluto10CA/TA driver along with the EDU2AE/TOP/TA control box. We have minimal experience in robotics and are trying to understand how to connect the control box to the robot.