@Ryan_Weaver can you share your experience with this integration?
https://www.youtube.com/watch?v=uaGXoWPUXJI


@gerenga what was your approach in the following integration?
https://www.youtube.com/watch?v=cTIdm5XpWf8
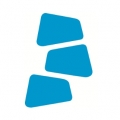
Any issues regarding the kolver system? I'm looking into an affordable system for my customers regarding proper torque control. However I find it rather difficult to find a system which allows to do proper tracking of the process regarding feedback to a quality control system. We use the robot absolute position to confirm full fastening as well but can you at the kolver system actually get a value or log to handle? Present programs are a good thing but I still look for a system to send actual parameters to the fastening unit. I'm nearly on a point to design our own system but don't want to reinvent the wheel if someone already has a solution which is doing the job.Ryan_Weaver said:Certainly @Samuel_Bouchard -
While using the infinite rotation on the UR3 Wrist 3 sounds appealing, it isn't very practical as a screwdriver. The torque resolution is very coarse and speed can be slow.
We decided to work with Kolver because they are a local company who offers a variety of screwdrivers, feeders and torque controllers at a very competitive price when compared to alternatives we had looked at. The speed/torque clutch out routines are stored in the controller, then called via I/O from the robot. That means you can handle multiple different screws without changing out tools as long as the bit is compatible. The pluto screwdriver is small, lightweight and was easy to design an interface plate for.
The actual application programming was pretty simple - standard UR force control takes care of the "screwing" action very well. The most challenging part was getting the screw feeder to present the screws in a repeatable position. The version we have in the video isn't truly a "robotic" feeder, it's meant for manual feeding by a person. In order for the screws to vibrate down the track, it has to be free standing, which means it can vibrate around on the table. The video gets the concept across, but in reality, we would probably use a feeder specialized for robots.
Thanks for the feedback.
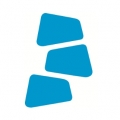
Still Thailand so budgets are often tight and we are still at industry 2.0 in many cases so we have to be more realistic about customer needs.Samuel_Bouchard said:@gerenga what was your approach in the following integration?
https://www.youtube.com/watch?v=cTIdm5XpWf8
Simple approach here is to show a first step low budget automation with UR.
Many of our customers already use a screw feeder and a auto screw driver so we wanted to show how easy it is to make the first automation step. Take a UR3, attached your available system, put your part in a jig where it usually is anyways and go.
In this case the customer has to invest only in the robot which makes the decision often easier. However beside it being a "quick & dirty" solution it has a few nice side effects.
Often the screw drivers are calibrated and there are fixed routing plans for the production procedure. We do not violate any of these so a lot of resistance for implementation doesn't happen in the first place as all the "nasty" documentation updates are not required to get going. Sometimes we have to make it as simple as that.
To market this further we just set up the application for the exhibition as people can relate to this process. However to not having to support this station in any way we decided that we want it running fully independent but screws in and out doesn't really show the repetitive action we wanted to show. So we decided to use a Zimmer group electric gripper and put the threads into the gripper fingers to show the Zimmer gripper precision as well. You may see some marks at the gripper finger threads but the counter was about 10,000 pieces when the video was done.
We have similar experience like Ryan regarding the manual screw feeder so we just locked it in place via aluminum profile still allowing vertical vibrations which fixed this issue.
We then had the topic that we wanted to show process control and a certain self diagnosis regarding our stations so we added a fiber optic sensor which confirms whether we actually picked up a screw because there is no interface between the screw feeder and the robot. However to make it a bit more obvious and fancy we relocated the sensor away from the pick up position to the side just for the show. In case the fiber optic sensor doesn't find a screw the robot will run another pick up cycle. Then we simply fasten the screw and beside checking the robot position when finished fastening, however to confirm that we don't actually still have a screw mounted on the tool when we go for another pick up run, we go to the sensor again and trigger a popup in case of detection to show self diagnosis functionality.
We are using the force mode as well as it is just that simple.
Once all screws are set, which is handled by variables in the robot program, the gripper opens and the screws fall back into the screw feeder. This is simply to keep the system running without the need to load or unload any material on the exhibition.
It's simple but effective.
Best regards,
Enrico

@yuvarajoo what are you using on your side?
https://www.youtube.com/watch?v=97mO2oa6Nsk
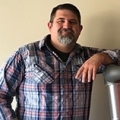
Sebastien said:@MKarabin this is really nice I am curious to know what feeder did you use for the screws. It seems to work well!
Looks like a system made by Kolver USA. http://www.kolverusa.com/products-list/12-Automatic-screw-supplier
@MKarabin how is the cost on this system? We have a couple opportunities that could benefit from a system like this
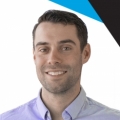
@yuvarajoo can you tell me which model you have been using? I would like to get that screwdriver to do some demo in our lab. thanks !
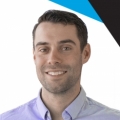
@yuvarajoo thanks!
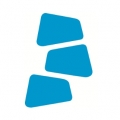
@Ryan_Weaver Thanks!
We have a customer looking to screw with a UR.
Is there any screwing gun that can be easily interfaced with the robot?
Electric screwdriver vs infinite rotation of the last joint, what to do and what not to do?