We use them for machine tending where the humans are stopping by on a regular basis and giving the robot more work to do and taking the completed work away from the robot. The collaboration between human and robot means we do not need to plan for lots of part storage or presentation systems. We may only put a few parts in front of the robot and and keep the cell simple. The humans can then spend more time checking on machines and inspecting parts while the robot does the mundane task of keeping the machine loaded and running. We do this with CNC's, punch presses, test equipment, laser engravers, cold form riveters, etc
We have applications where the human is assembling the parts and then the robot is fastening the part with either screws or rivets. let the human do the difficult task of lining everything up and ensuring it all fits together correctly, robot does the repetitive task of installing the fastener.
Dispensing sealants, humans presented parts to the robot which then very accurately dispensed the sealant onto the first part and then placed the next part onto the first very accurately. Reduced the amount of rework from about 10 minutes per part, cleaning up the part where the sealant leaked out due to inconsistent application by the human operator, to almost 0, most parts needed no cleaning, every once in a while a part would need a string wiped off.
Placing labels under a camera for vision inspection allowing the human operators to only need to look for things the machine vision system could not see easily, parts are being inspected for about 90 different features. Humans used to take about 30 seconds to do the inspection, robot does it in about 15 seconds, humans can do their part in just a few seconds now since they are only looking at a couple of features.
Taking a motor winding from an operator and trimming all of the wires to the correct length. Robot is much more accurate on the length of wire trim as well as we reduced potential for repetitive motion injuries on the line. Two robots then collaborated to transfer the motor to the final test line and then on to a conveyor that sent the motor to final inspection / pack-out.
Had another robot on the same line further upstream taking motor windings from the operator who loaded a basket and then loading that basket into the varnish tank/oven. Reduced the need for the operator to lift the basket (400 times a shift) as well as handle the hot basket when it came out of the oven.
Human placed heat shrink connectors onto motor leads, robot passed the leads under the heat gun. Humans did not have to be concerned with working around the heat gun or chance of being burnt any longer.
Those are just a few examples that I can think of.
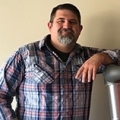
@Harish you're welcome
The potential application where man and robot need to work together for sure. Especially that is well suited for UR5 and UR3. When I think about this. Only bigger payload application come in my mind like Robot hold the heavy part and Human operator weld the parts. another example is the use of cobot in the assembly of heavy parts in the automotive industry. Please suggest some HRC application for lightweight robot.