@matthewd92
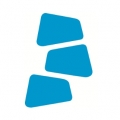

@Prasanna, there should be no compatibility issue when upgrading to 5.3 unless you have specific third party software installed (URCaps). Version 5.3 of the Polyscope software can be downloaded directly from the UR support website.
In addition to what @matthewd92 said, you can also use the get_tcp_force() function to get only specific forces or moments instead of the norm of the x-y-z forces.
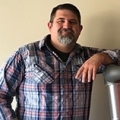
You’re welcome
i wanted to insert a piece into the slot and it is glass piece. So how can i use force function in order to prevent damaging or pushing the glass piece into the slot.
i do not have experience in Force Torque sensor and its functions.
also when exceeding particular force, the robot should switch to another subprogram.
Note: there is no Force Torque sensor attached. It is e series UR robot. Hope it comes along with FT sensor in its flange.