@YOSHIHISA have you looked into the controller online manual? Look into section 4 of the manual. Without anything plug, you should at least be able to read Byte 2 bit 4 to 7 who will return the fault status. Should return 0x00. What have you plugged into the controller?
Have you also double checked your IP address and communication settings? They can be found in section 3.5 of the manual
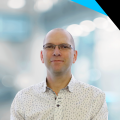
@YOSHIHISA
Modbus RTU is a Fieldbus protocol running over a serial com port. It could be RS-232, RS-422 or RS-485. It's the protocol running inside the gripper and we use an RS-485 line. Modbus TCP is derived from this protocol but running over an Ethernet connection. The protocol is slightly different. It's the goal of the Universal controller to convert the Modbus TCP protocol (PLC side) to the Modbus RTU protocol (gripper side). What is explained in the Gripper manual, it's the Modbus RTU protocol the gripper is using. If you would like to program yourself a standard Fieldbus protocol, you can find documentation about how they work on the web, but it absolutely not required. Normally, PLC have a lot of Fieldbus master device available like EtherCAT, Ethernet/IP, Profinet, Modbus TCP and then with the according Universal controller, gripper registers are then directly accessible in the PLC. Only the Fieldbus need to be configured. Fieldbus configuration file can be found on support web page here: https://robotiq.com/support/2f-85-2f-140. If you PLC support Modbus TCP then you are supposed to simply configure the registers of the gripper. If the PLC doesn't support the Modbus TCP, a suggest you to change to a Fieldbus your PLC support. If you absolutely want to program yourself this standard protocol. You can find some information on this website regarding the Modbus TCP protocol: http://www.simplymodbus.ca/TCP.htm
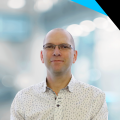
@YOSHIHISA
The two fingers gripper can connect directly to a Modbus RTU Master if the interface is RS-485. There is no need for a Universal Controller in between in this case. RS-485 settings are shown here:
https://robotiq.com/support/2f-85-2f-140/downloads-instruction-manual in section 4.7.1.
If your PLC has the Modbus RTU Master option, it will work. If not, it's going to be the hard way and you will have to program yourself this Standard Fieldbus protocol. The easy way will always be to have a Fieldbus <master> on a PLC to connect Fieldbus <slave> like the gripper or any other Fieldbus I/O.
Hi
I am trying communication between the PLC and Robotiq Universal Controller .
When reading is performed using the command of FC 03
Please also tell me the address to direct to the robot at the same time