Could you please provide more detail on the inspection requirement?
1. Inspection rate? How many labels per minute must be inspected?
2. Can the bottles be guided with side rails, etc. so that they are presented the same way every time? or are the bottles coming randomly?
3. If you can guide them for inspection, then what will the UR need to do? The vision inspection could be fixed mounted in this case.
4. Could then the rejects be diverted to another belt without the UR as well?
Hello everyone,

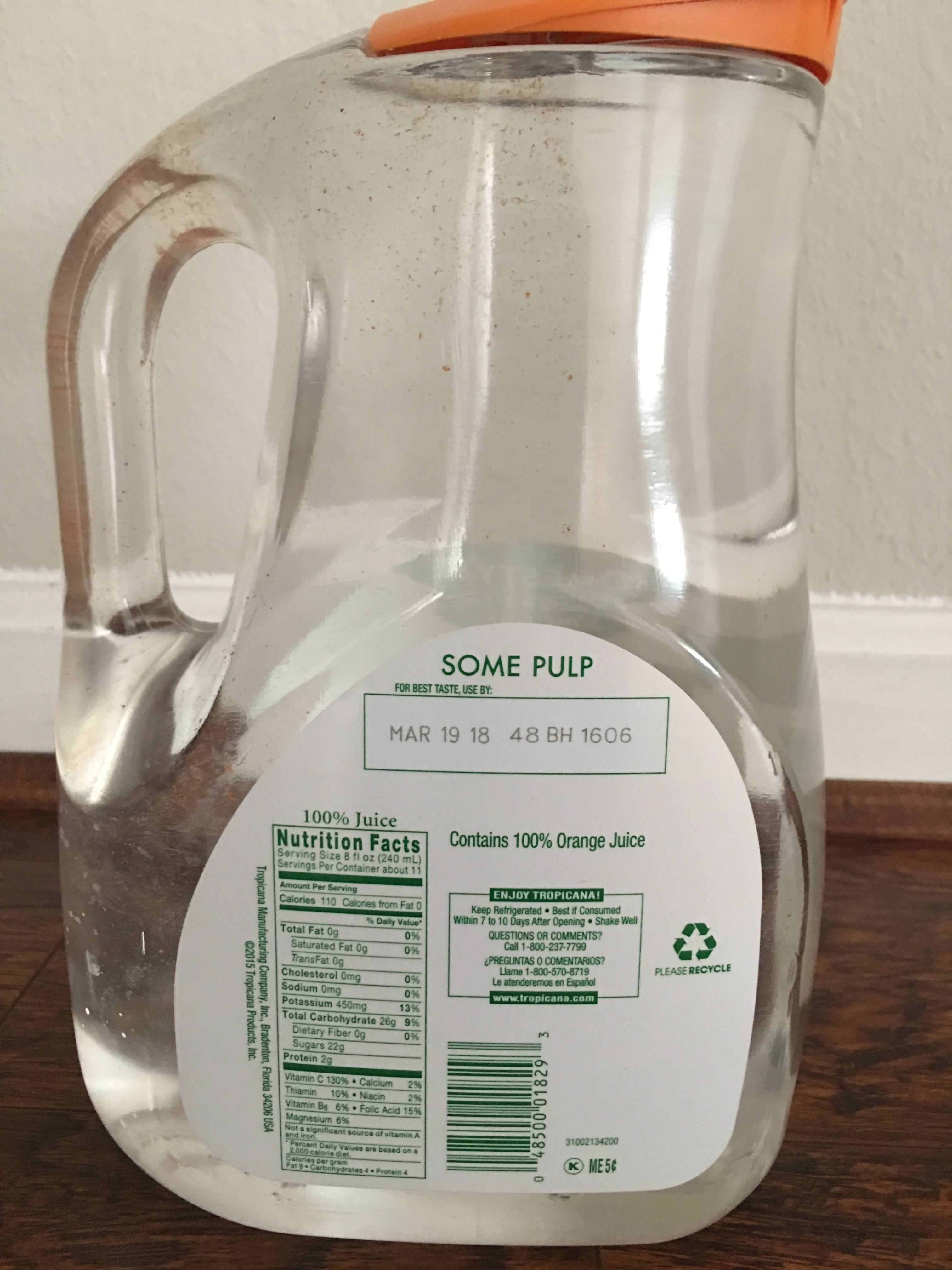
I wanted to reach out to the eclectic perspectives of the DoF community for some guidance on a potential UR 10 application. I'm seeking multiple solutions in order to determine which is the most effective and feasible.
The basis of the application would be to have the UR 10 grab a product off a moving conveyor and interface with some vision system in order to verify the consistency and quality of the front and rear label.
The points of consideration are:
The overall approach, integration strategy, and all components necessary to implement a label inspection collaborative robot cell with the capability to attain or surpass the performance of a human operator.
Which vision sensor should be used and how should the sensor be mounted?
How should the vision sensor and the UR 10 interact so that both the front and rear label can be inspected in a consistent manner?
Implementing conveyor tracking versus stopping the line momentarily
Gripper strategies in order to grab the product in the same manner each time on a moving conveyor
How to handle the pass and fail products: should a secondary line be implemented because of the difficulty in having the UR 10 place passed products back onto a moving conveyor
The images below are similar to the products that will be handled.