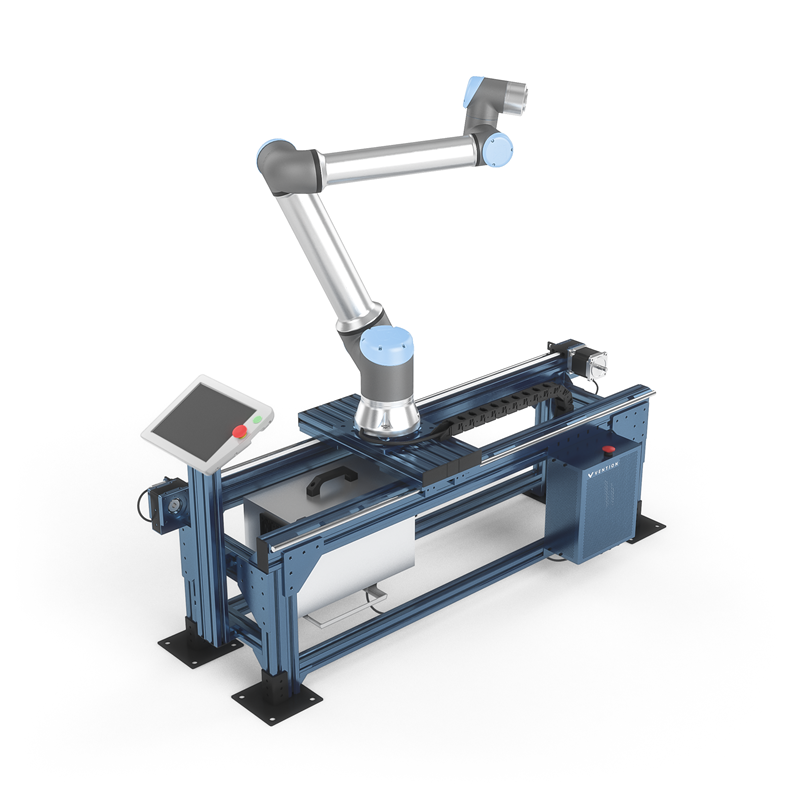
@Sebastien do you need to be moving the robot while you're moving the slide or is it move to one end and do some work then move to the other end and do some work there? We've looked at a couple of applications that needed a slide as well and have done a little noodling around how to make it work.
I do wish that UR would allow for 7th axis control like other robots.
Hi pros,
we haven't search much yet into that topic and my first was to ask you guys if you done something like this. We are currently looking at a project where the UR would need to be moved on a rail. So far it is quite easy as the rail will have only two positions (one at each end). So the integration is quite simple.
However I was curious to see how hard would it be to have the UR move on a servo driven axis? We are used to work with this on Fanuc robot where the axis is integrated to the system such that when you move a 6 axis robot on a rail, on the teach pendant there are 7 axis to move. So when you teach points, they record all 7 axis values. I am guessing that it would be feasible to make this work on UR but could be tricky. What do you think? Any experience you are willing to share?